 |
 |
|
 |
|
 |
|  |
|  |
|
 |
|
 |
|  |
|  |
|
 |
Thomas de Groot <tho### [at] degroot org> wrote:
> Op 05/03/2023 om 07:27 schreef jr:
> > hi,
> >
> > "Bald Eagle" <cre### [at] netscape net> wrote:
> >> ...
> >> Here's a sort of uv-unwrapped render of the outer and inner surfaces, ...
> >
> > wow, neat. (what do you (collective) make of the interior? paint?)
> >
> >
> LOL. I noticed (on the models) that the inside mesh is not complete. I
> guess the vase opening was too small for the scanner.
>
> --
> Thomas
Yeah, I'm guessing that it's just a partial mesh, which is a pity. Maybe
someone will be able to do another, more complete scan of it.
I was trying to fiddle with the locations of the key features and was tired of
working blind, so I wanted a nice easy-to-see format for the inner and outer
surfaces.
- BW
Post a reply to this message
|
 |
|  |
|  |
|
 |
From: Thomas de Groot
Subject: Re: Request: HIGH resolution stl conversion to mesh / mesh2
Date: 6 Mar 2023 02:47:07
Message: <64059a7b@news.povray.org>
|
|
 |
|  |
|  |
|
 |
Op 05/03/2023 om 22:18 schreef Bald Eagle:
> Thomas de Groot <tho### [at] degroot org> wrote:
>> Op 05/03/2023 om 07:27 schreef jr:
>>> hi,
>>>
>>> "Bald Eagle" <cre### [at] netscape net> wrote:
>>>> ...
>>>> Here's a sort of uv-unwrapped render of the outer and inner surfaces, ...
>>>
>>> wow, neat. (what do you (collective) make of the interior? paint?)
>>>
>>>
>> LOL. I noticed (on the models) that the inside mesh is not complete. I
>> guess the vase opening was too small for the scanner.
>>
>> --
>> Thomas
>
> Yeah, I'm guessing that it's just a partial mesh, which is a pity. Maybe
> someone will be able to do another, more complete scan of it.
>
> I was trying to fiddle with the locations of the key features and was tired of
> working blind, so I wanted a nice easy-to-see format for the inner and outer
> surfaces.
>
I can try to slice it using Silo. Just to see how it looks inside...
--
Thomas
Post a reply to this message
|
 |
|  |
|  |
|
 |
|
 |
|  |
|  |
|
 |
Thomas de Groot <tho### [at] degroot org> wrote:
> I can try to slice it using Silo. Just to see how it looks inside...
I don't see why not.
Ben states that they were unable to scan the interior of the vessel, due to the
limitations of the structured light scanning instrumentation.
They also play around a bit with the mesh and some primitives using Blender.
https://www.youtube.com/watch?v=SQMSGkZIfao
One very interesting point that brought up is the seemingly anomalous lack of
accuracy in the lug handle holes. Ben points out that, given there are a large
number of examples of vessels that have no holes whatsoever, that the vase may
have been manufactured without holes, and someone (less skilled) added the holes
later.
Apparently there has been some small bit of controversy between the two main
post-metrology analysts regarding reference points, proportions, and what is
real regarding various dimensions lines and ratios.
It might be interesting to develop a parameterized vessel composed entirely of
primitives as a sort of playground, that can them be exported as a mesh for
comparison in CloudCompare, Polyworks, or other more sophisticated software.
Has anyone opened it in MeshLab to see what sorts of measurement and analysis
tools are available there?
- BW
Post a reply to this message
|
 |
|  |
|  |
|
 |
From: Thomas de Groot
Subject: Re: Request: HIGH resolution stl conversion to mesh / mesh2
Date: 6 Mar 2023 11:39:04
Message: <64061728@news.povray.org>
|
|
 |
|  |
|  |
|
 |
Op 6-3-2023 om 12:44 schreef Bald Eagle:
> Thomas de Groot <tho### [at] degroot org> wrote:
>
>> I can try to slice it using Silo. Just to see how it looks inside...
>
> I don't see why not.
>
OK. So, I started fresh from the original STL file. Silo can import it,
but it is too heavy for the program to cut it up. I did however a couple
of basic transformations to align the mesh to the world axis.
Answering here your question below: I could load the STL into MeshLab
and could easily simplify the mesh and convert it too quads within
minutes. I am not too familiar with MeshLab but I guess there are a lot
possibilities there that can be applied. I shall investigate further.
> Ben states that they were unable to scan the interior of the vessel, due to the
> limitations of the structured light scanning instrumentation.
>
> They also play around a bit with the mesh and some primitives using Blender.
>
> https://www.youtube.com/watch?v=SQMSGkZIfao
>
> One very interesting point that brought up is the seemingly anomalous lack of
> accuracy in the lug handle holes. Ben points out that, given there are a large
> number of examples of vessels that have no holes whatsoever, that the vase may
> have been manufactured without holes, and someone (less skilled) added the holes
> later.
>
I find this a bit strange but that may be true. The vases were made as
funerary furniture as far as I know and perhaps - depending on your
wealth - the objects were more or less finished? In the digs all kinds
of (un)finished states were found.
> Apparently there has been some small bit of controversy between the two main
> post-metrology analysts regarding reference points, proportions, and what is
> real regarding various dimensions lines and ratios.
>
> It might be interesting to develop a parameterized vessel composed entirely of
> primitives as a sort of playground, that can them be exported as a mesh for
> comparison in CloudCompare, Polyworks, or other more sophisticated software.
>
yes.
> Has anyone opened it in MeshLab to see what sorts of measurement and analysis
> tools are available there?
>
See above.
I attach a few screenshots from the STL in Silo. I had not fully
realised this but the whole base has not been scanned and there is that
mess of the inside well-visible here.
--
Thomas
Post a reply to this message
Attachments:
Download 'vase_stl_01.jpg' (33 KB)
Download 'vase_stl_02.jpg' (47 KB)
Download 'vase_stl_03.jpg' (413 KB)
Preview of image 'vase_stl_01.jpg'
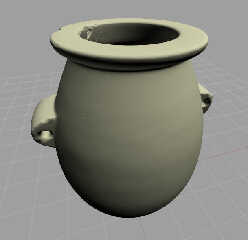
Preview of image 'vase_stl_02.jpg'
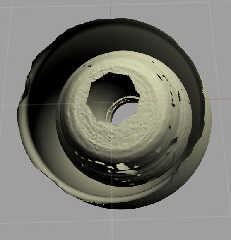
Preview of image 'vase_stl_03.jpg'
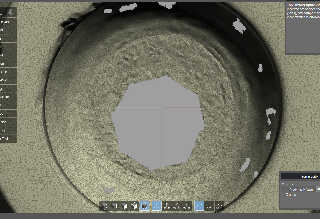
|
 |
|  |
|  |
|
 |
|
 |
|  |
|  |
|
 |
"Bald Eagle" <cre### [at] netscape net> wrote:
> Hi folks,
>
> Ben from UnchartedX has just posted the stl file from a professional
> metrological scan of a pre-dynastic rose quartz vase.
>...
> The file is 44.6 MB, and it would be great if someone could convert it to a mesh
> {} or preferably mesh2 {} object. You could likely post it on a free
> file-hosting service for the next 30 days like I did with F. Lohmueller's
> (partial) web archive.
>
>
https://unchartedx.com/site/2023/02/19/new-video-updates-to-the-vase-scan-responses-and-the-stl-file/
Hi Bill
That's a very interesting vase.
I just wrote a little Python script using numpy and numpy-stl to
extract the 473864 unique vertices from the STL file and store them
and the corresponding face indices in arrays in a POV-Ray .inc file.
(The number of non unique vertices in the STL file is 2811429.)
Here's a rendering with triangles, cylinders and spheres made with
data from that .inc file, showing the details around one of the
handles on the vase.
--
Tor Olav
http://subcube.com
https://github.com/t-o-k
Post a reply to this message
Attachments:
Download 'vasetest _ 06.jpg' (1158 KB)
Preview of image 'vasetest _ 06.jpg'
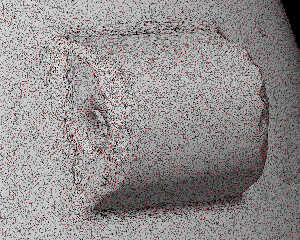
|
 |
|  |
|  |
|
 |
|
 |
|  |
|  |
|
 |
"Tor Olav Kristensen" <tor### [at] TOBEREMOVEDgmail com> wrote:
> Hi Bill
>
> That's a very interesting vase.
There's a lot of interesting items that they've discovered, and the ridiculous
level of accuracy and tight tolerances in such a hard and heterogeneous material
raises a LOT of questions.
> I just wrote a little Python script using numpy and numpy-stl to
> extract the 473864 unique vertices from the STL file and store them
> and the corresponding face indices in arrays in a POV-Ray .inc file.
> (The number of non unique vertices in the STL file is 2811429.)
Hmmm. Very nice.
1. how large is your .inc file?
2. can you make that into a mesh2 {} ? Will that make the file size smaller?
3. would it be possible without undue work to number (with comments) the unique
vertices and correlate the redundant vertices with the ones in actual use?
(listing them all at the end of the file in a large en-bloc comment and marking
them with the numbered vertex that they are a duplicate of)
I only bring these things up because if you did such a thing and posted that
file here on the POV-Ray forums, it might generate some new traffic and
potentially bring in some new users to discover what POV-Ray has to offer.
> Here's a rendering with triangles, cylinders and spheres made with
> data from that .inc file, showing the details around one of the
> handles on the vase.
That is certainly a LOT of triangles.
I don't know if you've looked at the article by Mark Qvist posted here:
https://unsigned.io/granite-artifact/
RTI?
https://twitter.com/mariusderomanu3
I've been curious about the vertex coordinates that Mark is using for his
diagrams, and what sorts of tools would be best suited to replicating or
obtaining a truer-to-reality analysis of the surface features. Maybe some kind
of least-squares best fit, or some way of determining which points a line would
be "tangent" to on both the rim and lug handle.
There really are a lot of different dimensions and geometric relationships to
investigate. I'm really hoping that they are able to obtain a complete mesh of
the vessel as well as doing some microscopic / spectroscopic analyses of the
surface to see if any residues of the work-holding fixture or tooling remain
embedded in the surface.
Thanks for taking a look and processing all those vertices. I'm curious what
your thoughts are about the vase in general, as well as what sorts of analyses
you think might be interesting to perform, and what sorts of POV-Ray fun could
be had with it.
- BW
Post a reply to this message
|
 |
|  |
|  |
|
 |
|
 |
|  |
|  |
|
 |
So, I remembered that a very fast way to analyze the curvature of a surface is
with a "zebra line" lighting setup, and so I applied that to a vase with a
mirror finish.
Nothing amazing really popped out at me, but it does show that other than some
of the 5000 years of wear, it's a very evenly curved surface.
Post a reply to this message
Attachments:
Download 'vasecurvaturelines.png' (175 KB)
Preview of image 'vasecurvaturelines.png'
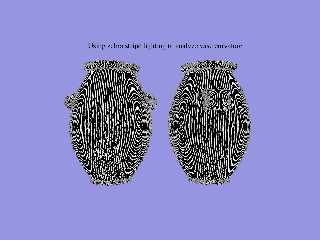
|
 |
|  |
|  |
|
 |
|
 |
|  |
|  |
|
 |
Freya Holmer, working on the same topic, discovered that industries also use a
pattern of dots to look at curvature as well, and so I gave that a go.
I might have to experiment more with scales and such to see if anything
interesting happens.
Post a reply to this message
Attachments:
Download 'vasecurvaturespots.png' (196 KB)
Preview of image 'vasecurvaturespots.png'
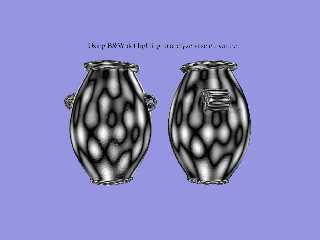
|
 |
|  |
|  |
|
 |
|
 |
|  |
|  |
|
 |
vase:
There are a few things that occurred to me, inspiring a few ideas to explore and
either confirm or refute their merit.
1. Given that there is all of this "sacred geometry" stuff that people go on
about, what is it's origin and why?
I think that we are taking a look at objects and structures that are designed
using a method much like we use CAD, however I think we can agree that the
ancients didn't have computers as we know them, and they probably used an
absolute measurement system different than our own.
But what makes absolute units irrelevant, and simultaneously preserves the
constants that we see?
Relative measurements. In geometry class, everything is laid out with a compass
and straightedge, and nothing is measured in "units". But everything is
measured in relation to line segment lengths, radii, etc.
The Greeks apparently got a lot of their knowledge from the Egyptians, and so
this comports with what we (think we) know about history.
2. If the designers used a well-developed system to lay out the design
parameters of objects and structures, and it was a relative system, then it
seems likely that they made use of all of the methods used in standard geometry.
Things would be laid out using arcs and lines and ratios. Pi would naturally
show up everywhere because ... circles.
3. Alex Dunn and Nick Sierra used a sphere in their metrological analysis - not
because they were trying to show that a sphere in any way "matched" the surface
of the vase, but more to show that the distance of the surface to the ideal
sphere was very constant along the vertical axis (among other reasons).
You showed that the overall vase shape deviates from an ellipsoid with your
overlay.
It occurred to me that if I was going to build a machine with a tooling guide
that was inspired by classical geometrical methods, then I'd use a lot of
circular arcs. Which led me to think that the vase might more strongly resemble
a vesica piscis, or when the circle centers do not lie on the the other circle,
what is called a geometrical lemon. This is also exactly the inner surface of a
spindle torus.
I've spent a lot of time developing some macros for use in fitting circles and
spheres to measured data sets, and coming up with a way to compare the vase to
the lemon shape. Fortunately, POV-Ray has some inbuilt functions and primitives
that ultimately make that task a lot simpler, and I was able to devise a 3D
texturing pattern that is essentially an unsigned distance function of the
lemon. By applying this pattern to the vase mesh, it maps the closeness of fit
of the mesh to the lemon.
The result is obviously sensitive to the radii of the generating torus, as well
as the vertical positioning of the pattern. I used the data from your recent
Twitter post to estimate the arc of the side of the vase, and using the chord
length and depth of that putative circle segment, calculated the radius of the
required circle. I used the vertical height of the maximal external radius of
the vase, since that made the most sense, in terms of the machining operation.
(I'm going to try to use the data points from scanning the vase to fit a circle
using the least-squares stuff, and see what happens with that)
****
And here's what's interesting: The curvature/shape of the vase seems to be
reasonably consistent with that below the handles, and only deviates above that.
Of course, that's as far as a tool traveling along a fixed arc could make it
before beginning to machine away the torus that would eventually give rise to
the handles. Also, the only significant deviation from that curvature is right
along the centerline of the two circles.
Owning a lathe myself, this would typically be the area that an operator is most
likely to accidentally come in contact with, either with a tool, the tool
support, or some other fixture or tool being moved in close proximity to the
spinning work.
4. I think it might be a prudent change of tactics to think about how the vase
would have been machined - the order of operations, and see if that inspires any
new ideas and areas of investigation.
Post a reply to this message
Attachments:
Download 'vaselemoncomparison.png' (1167 KB)
Preview of image 'vaselemoncomparison.png'
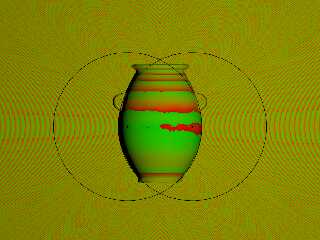
|
 |
|  |
|  |
|
 |
From: Thomas de Groot
Subject: Re: Request: HIGH resolution stl conversion to mesh / mesh2
Date: 13 Mar 2023 03:24:00
Message: <640ecf90$1@news.povray.org>
|
|
 |
|  |
|  |
|
 |
Op 12/03/2023 om 18:46 schreef Bald Eagle:
> I've been going over this a bit with, and following the excellent work of Marián
> Marčiš, and I just sent him this email regarding my most recent work on the
> vase:
>
That is a *very* good comment Bill. Thanks for sharing.
I don't know if you know the archaeological work at the Apollo Temple in
Dydima, Turkey. Scratched on the inner walls of the sanctuary are the
faint outlines of the construction plans made by the architects, and
they did use geometry pretty close to what you describe. The same for
the columns (some very subtle design indeed!) etc. No 'magic' was used!
;-) ...and neither did I when I modelled the temple in Moray, Silo, and
finally POV.
In other Ancient World sites identical architectural plans have been
found, e.g. in Rome.
It has been a long while since I read up on this (20+ years) and I don't
know if I still have documentation about these matters. I shall investigate.
--
Thomas
Post a reply to this message
|
 |
|  |
|  |
|
 |
|
 |
|  |
|
 |